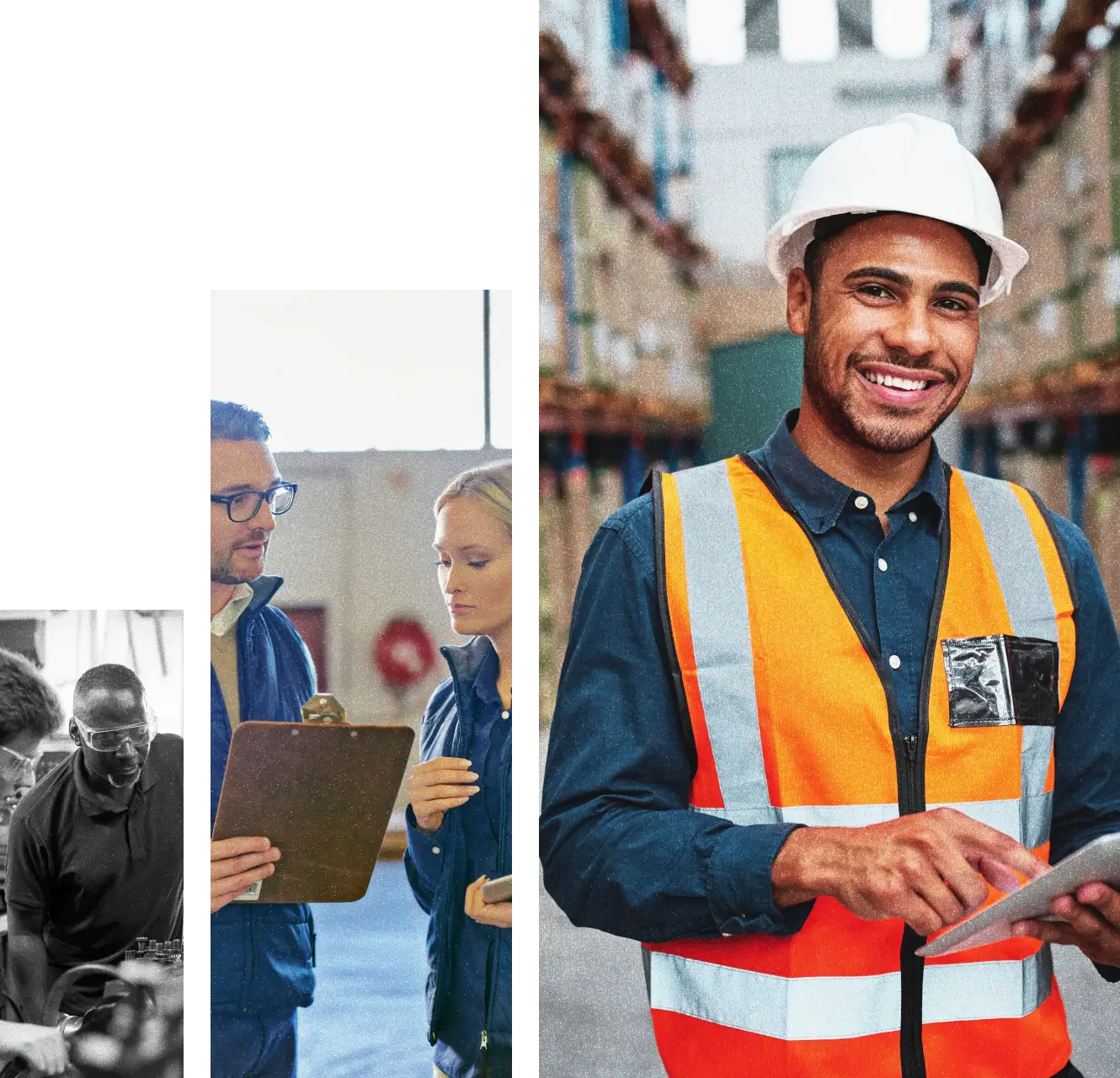
Discover a Path to Growth with Manufacture Nevada
We are committed to helping you succeed, not with a list of prescribed to-dos, but by getting to know your business intimately and sharing our deep understanding of modern manufacturing processes, business strategies and workforce management. We work shoulder-to-shoulder with you to determine a path to success and implement strategies that grow your business.
01 Step One
Connect with a Manufacturing Business Advisor
The first step is connecting with one of our advisors. Through a call or site visit, they will do a deep dive on your business, seeking to understand your processes, people, and problems to better lay a foundation for strategy.
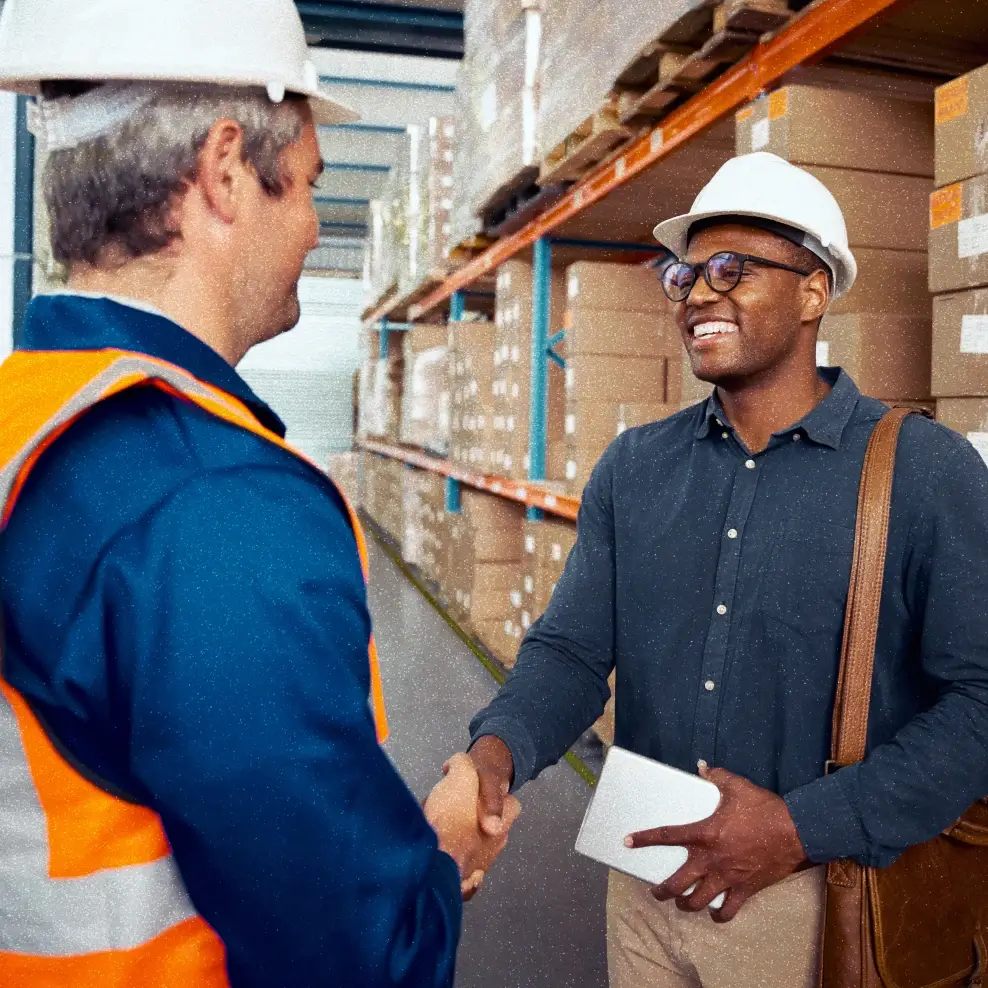
02 Step Two
Scope of Work & Evaluation
Once we’ve established a list of possible projects, we will help you establish a plan of attack for your biggest problems and determine the desired result of our project together.
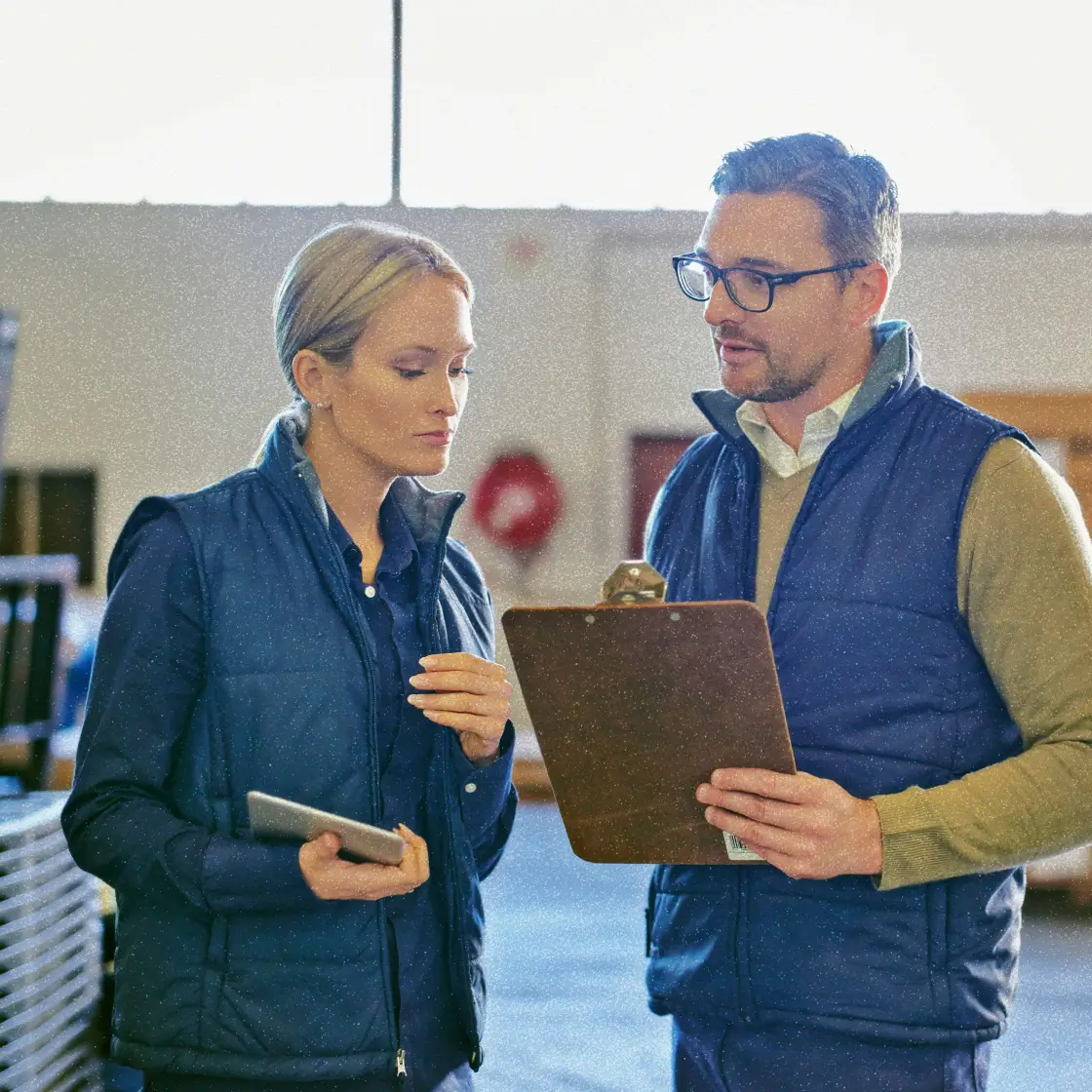
03 Step Three
Implement for Success
Once planning is finished, we will help you implement solutions to reach the desired outcome. Through regular contact with project managers and our expert team of advisors we will track milestones and set you up for long-term success.
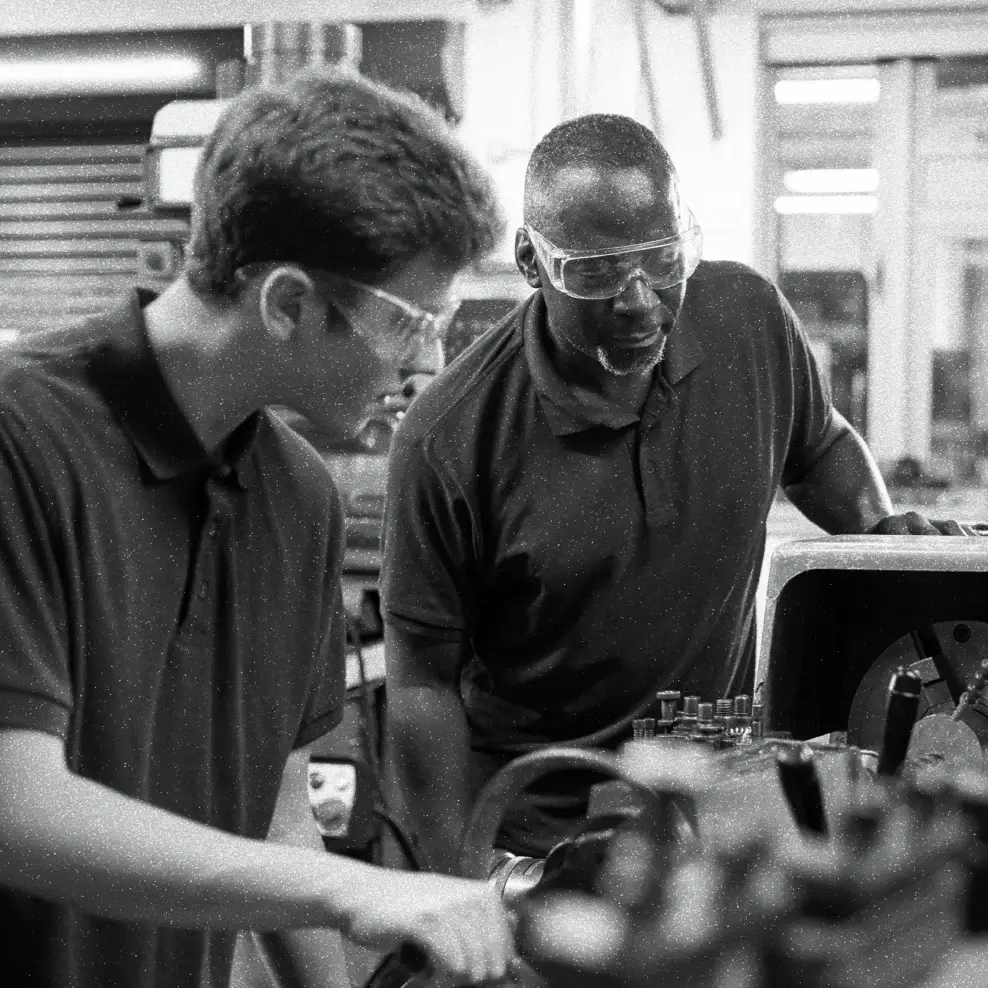
04 Step Four
Project Evaluation & Continuous Improvement
The first thing we do at the end of a project is determine how successful our efforts have been. From there we can determine if it would be beneficial to start a new project, or employ additional resources to reach your desired outcomes.
We work to create an environment of continuous improvement so that the benefits of our partnership don’t disappear after our involvement has ended. Your continued success is the defining factor of a successful project with Manufacture Nevada.
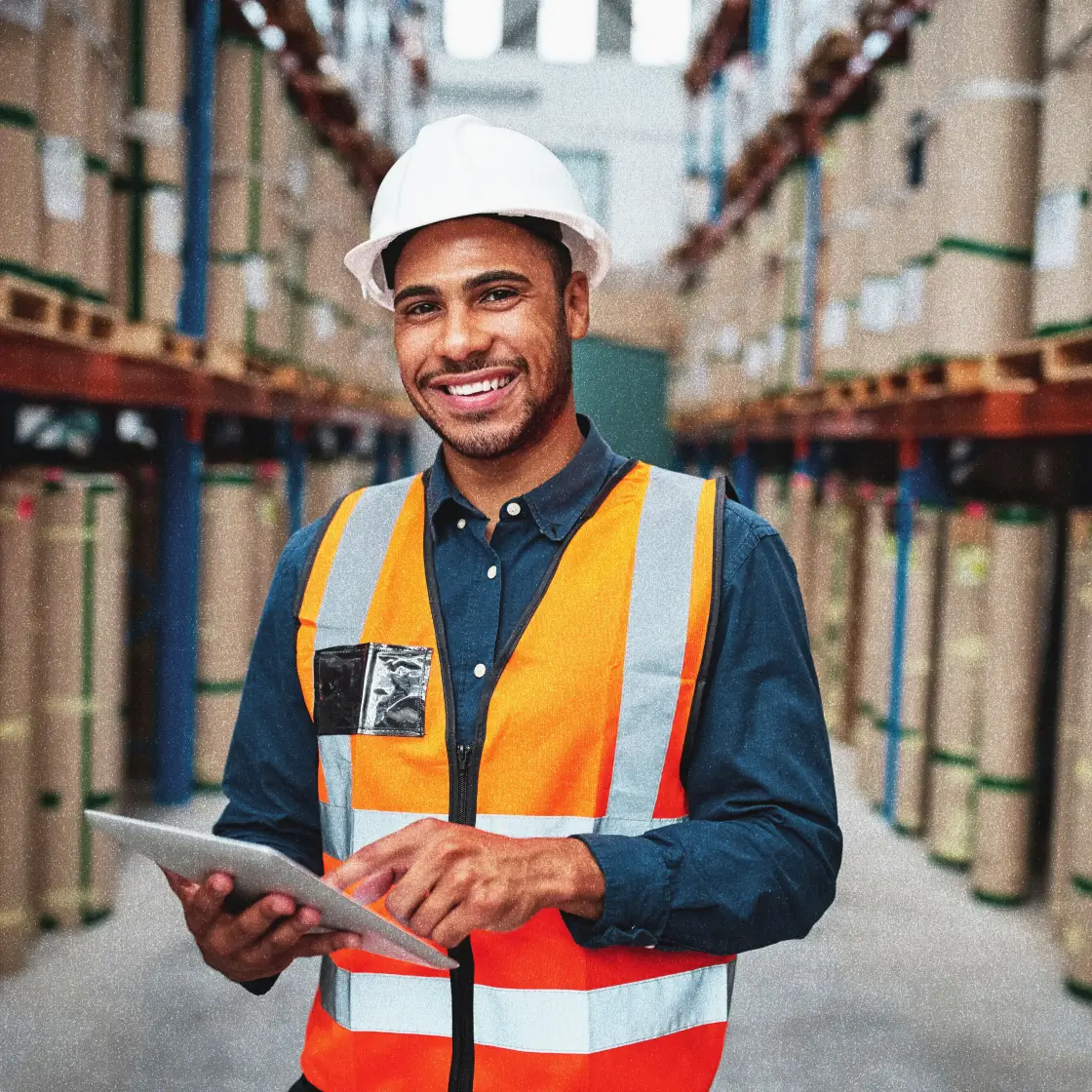
Take the First Step
Get in contact with a Manufacture Nevada representative to discuss
reaching your growth targets.