Strategies to Train, Upskill, & Engage Your Workforce
Do these challenges sound familiar?
You want to provide fulfilling careers to your team.
It takes too long to train people.
You need capable people ready to make decisions while you are away.
You want your managers to be successful leaders.
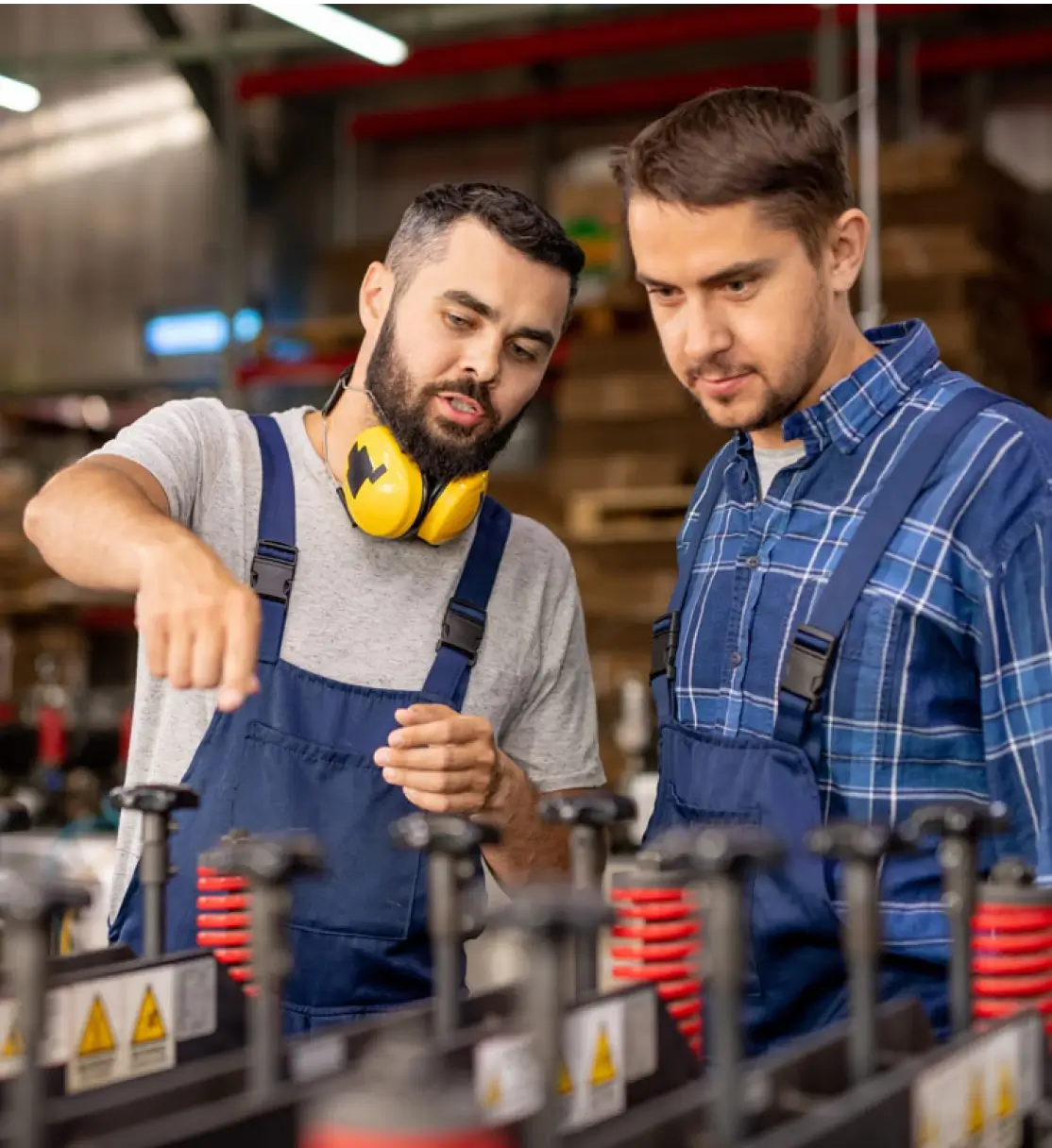
Trusted by Hundreds of Manufacturers Across Nevada
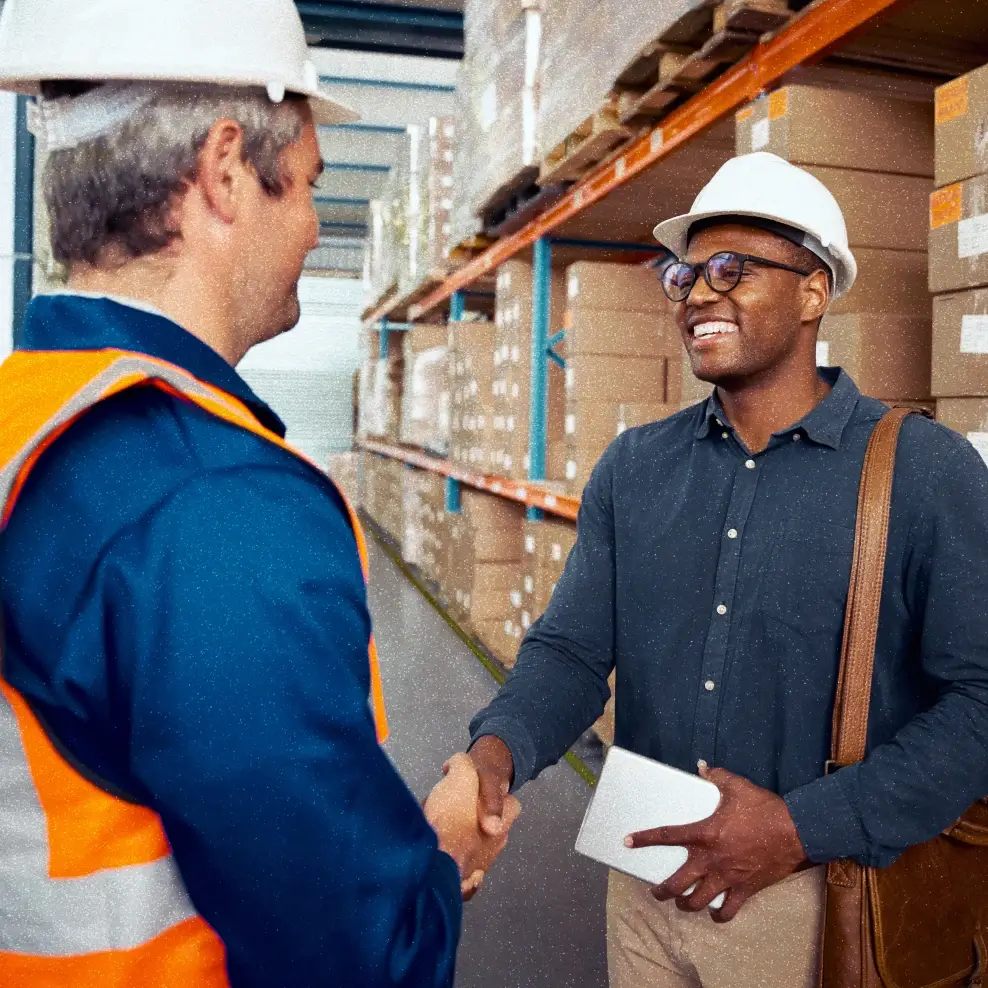
Help Employees Grow Their Skills
Your team is the key to the success of your business. Watch your best workers become your best supervisors, and your whole team drive more efficiency on the shop floor through our training programs and network of training resources.
“Nevada Industry Excellence has consistently responded to our manufacturing, process improvement and employee development requests. Manufacture Nevada’s portfolio of services and experienced resources have been a fit to our needs in supporting and improving, both our current and future growth demands.”
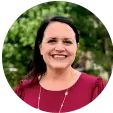
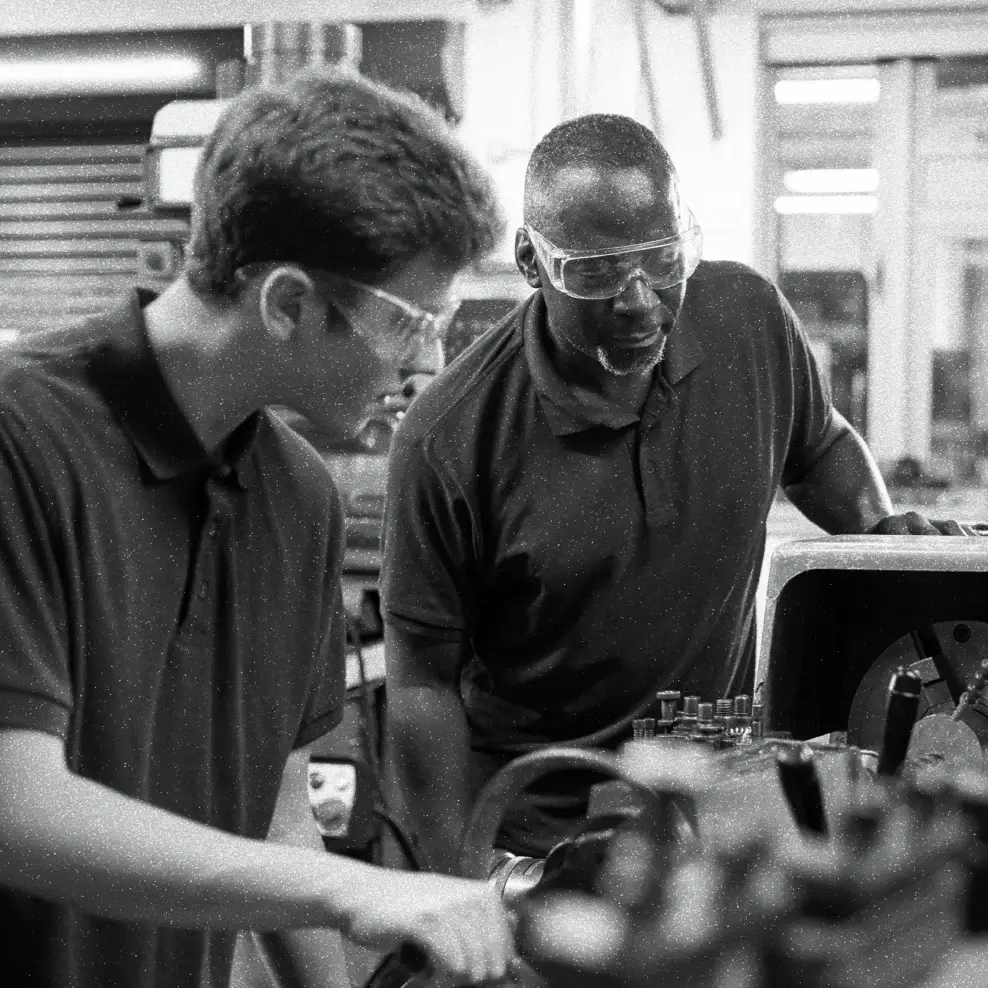
Keep & Train Your Best Employees
Turnover can be one of the most costly threats to a manufacturing business. We develop tailored strategies that improve employee job satisfaction and upskill your best workers, so they stick around for the long haul.
“Manufacture Nevada is an amazing resource. Pure Gold.”
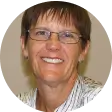
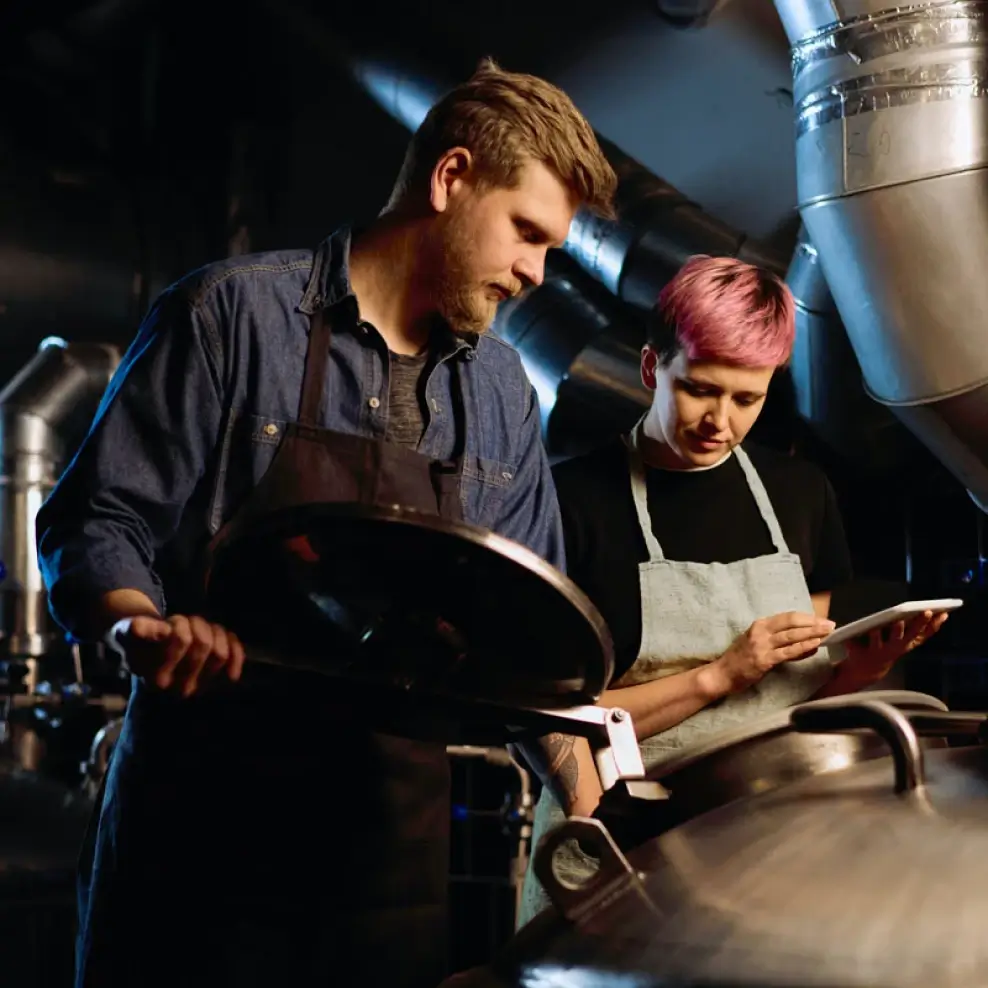
Help Your Employees Reach Their Full Potential
Poor time utilization can cause low morale and lead to poor team performance. Let’s work together to develop strategies to ensure your workers reach their full potential – improving your workforce’s efficiency and job satisfaction.
“Manufacture Nevada’s training and expertise in lean manufacturing provided the right tools at the right time to help grow our new product line and fit it into our existing facility. Our new Bio Cart is now a standardized product that is ready to dominate the market!”
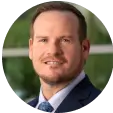
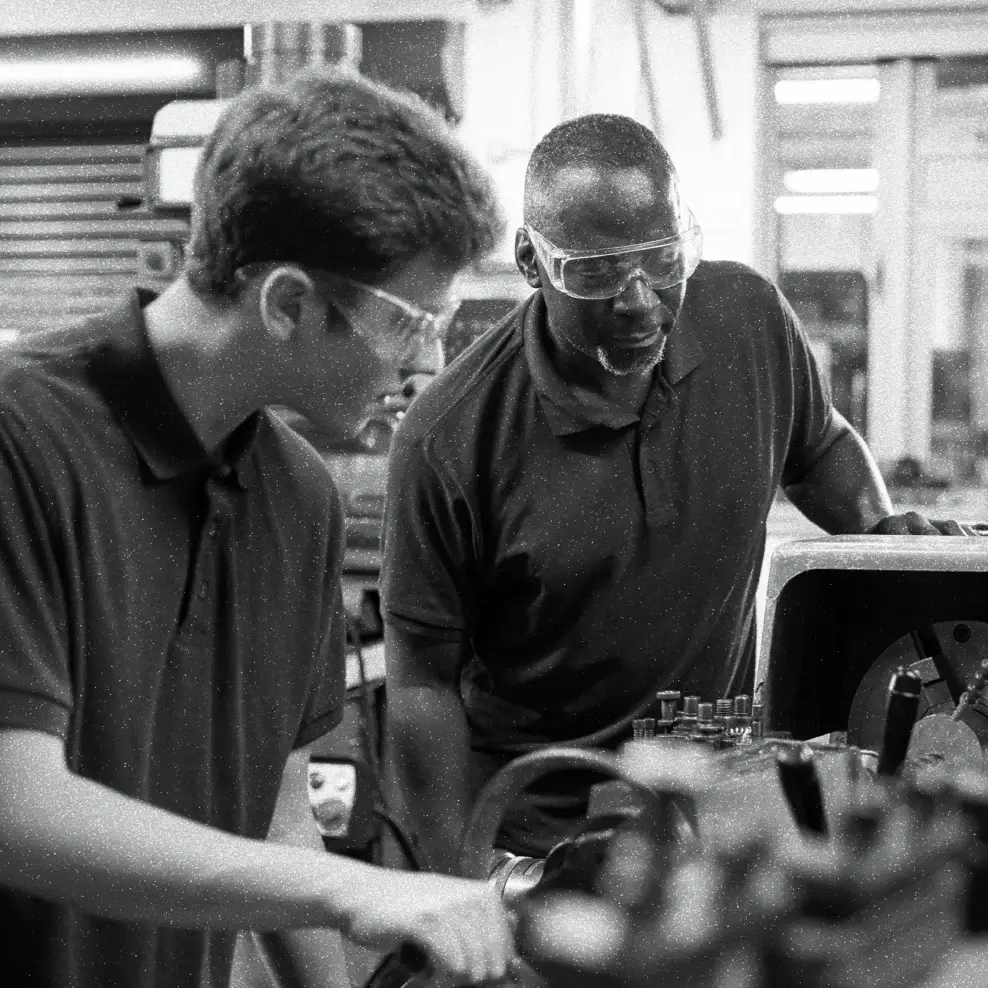
Define & Create the Culture You Want in Your Workplace
Create a business people want to work for. Together, we can determine what it means to be a part of your company and equip your managers with the tools they need to align your whole workforce with the new vision.
"It used to be maybe an idea would get tossed out and people would say we have done it this way for 15 or 20 years, why should we change? Now our workers have set up lean manufacturing cellularized lines and let the employees design the lines and take ownership of it because it is theirs.”
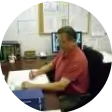
Take the First Step
Get in contact with a Manufacture Nevada representative to discuss
reaching your growth targets.